切缝宽度铜钨合金( CuW) 兼有铜( Cu) 的高导热性、钨 (W) 的高熔点、低热胀系数及耐电火花侵蚀能力强的特点,是一种高性能、低损耗的工具电极材料, 广泛应用于微细、精密电火花成形及硬质合金、钛合金等难加工材料的电火花成形加工中[ 1- 3] 。针对某些具有窄缝( 缝宽< 0. 5 mm) 、清棱清角或高纵横比结构的成形电极, 传统切削加工显然已不能满足加工要求, 实际应用中多采用低速走丝电火花线切割加割加工相对于传统加工, 有助于提高贵重合金材料的利用率。
多次切割技术是低速走丝电火花线切割加工实现精密加工的主要工艺手段。其中第一次切割去除了绝大部分加工材料, 在整个加工过程中占用了大量的切割时间。同时, 第一次切割加工尺寸精度的提高及表面粗糙度值的降低, 可在达到相同加工目标的情况下减少切割次数, 成倍地提高加工效率、降低加工成本。
电火花线切割加工过程中的电极丝运动轨迹相对于编程轨迹有一定的偏移量。电极丝偏移量及其自身的振动影响着切缝的宽度尺寸, 进而影响加工的尺寸精度, 稳定的切缝宽度是实现高尺寸精度加工的前提条件。针对影响线切割切缝宽度的因素,研究人员分别基于正交试验与单因素实验, 在方差分析与理论分析的基础上发现开路电压是影响切缝宽度最显著的因素[ 4- 5] 。Rakwal 基于正交实验与方差分析, 发现放电电容是影响切缝宽度最显著的因素[ 6] ; Shah 通过正交试验与方差分析发现, 脉冲时间与电极丝张紧力是影响切缝宽度最显著的因素,开路电压与脉冲间隔对切割宽度影响较弱[ 7]; Mahapatra通过正交试验与方差分析发现, 走丝速度是影响切缝宽度最显著的因素[ 8] 。可见, 研究人员在影响切缝宽度的因素分析中尚未得到统一的结论。
在加工铜、钢及硬质合金等方面, 线切割加工工艺已日趋成熟, 但目前人们对铜钨合金电火花线切割加工的研究还较匮乏。本文以铜钨合金为加工材料, 研究了各加工参数对线切割加工第一次切割的切缝宽度、加工速度及表面粗糙度的影响规律, 为实际加工提供理论指导。
1 实验过程
实验在三菱电机数控精密低速走丝线切割机床上进行, 电极丝选用直径0. 2 mm 的黄铜丝, 电介质为去离子水, 电阻率为10 万8#cm, 上下喷嘴距工件距离均为0. 2 mm, 加工材料为厚度6 mm 的铜钨合金( 质量分数Cu 30 %, W 70 % ) , 切割长度为20mm。
电火花线切割加工是一个多参数输入、输出的复杂过程, 影响其加工指标的因素可分为电参数与非电参数两类。本文通过大量单因素实验, 重点研究了伺服基准电压( VG) 、开路电压( VO) 、峰值电流 ( IP) 、脉冲间隔( OFF) 、电极丝张紧力(WT) 及走丝速度(WS) 对线切割切缝宽度、平均加工速度及切缝表面粗糙度的影响规律。其中, 各影响因素的大小并非实际值, 而是机床相应的档数。
实验中切缝宽度由工具显微镜测量, 对加工后的各切缝均匀间隔选取12 个位置测量, 求其均值作为最终切缝宽度; 由加工时间直接反映平均加工速度, 加工时间越长, 平均加工速度越慢; 表面粗糙度由探针式表面粗糙度仪测得, 各切缝表面测量2 次取均值。
2 实验结果与数据分析
2. 1 切缝宽度的影响因素分析
图1 是电火花线切割加工中切缝宽度的构成示意图。当电极丝与工件之间的距离达到电介质击穿距离时, 两极间产生火花放电, 同时柔性电极丝在放电力、静电力及冲液压力的共同作用下产生一定振幅的振动, 因此, 电火花线切割切缝主要由电极丝直径、放电间隙、电极丝最大振幅三部分组成, 可表示为:
W= D+ 2( A+ d )
式中: W 为切缝宽度; D 为电极丝直径; A 为电极丝最大振幅; d 为放电间隙。
低速走丝电火花线切割加工中的电极丝为单向走丝、单次使用, 电极丝损耗对切缝宽度变化的影响可忽略, 在不更换电极丝的情况下, 各加工参数对切缝宽度的影响主要是由于放电间隙及电极丝振幅而引起的。
图2 是各因素对切缝宽度的影响规律曲线。从图中可看出, 伺服基准电压、峰值电流、电极丝张紧力对切缝宽度的影响显著, 而开路电压、脉冲间隔及走丝速度对切缝宽度影响较弱。在一定范围内, VG与IP 的增加都会引起电极丝与工件之间平均放电能量的增加, 进而增大放电间隙, 引起切缝宽度显著增大; 电极丝张紧力的增加则会缩小电极丝振幅,减小切缝宽度。反之, VG 与IP 减小, 切缝宽度减小; WT 减小, 切缝宽度增加。但是, 当VG 过小时, 切缝宽度大幅减小的同时会造成电蚀产物排除困难, 电极丝与工件短路频率增加, 电极丝与工件频繁接触而引起断丝, 导致无法加工; 当VG 过大时, 虽不会断丝, 但电极丝与工件间出现开路状态的频率增大,有效放电次数减少, 平均放电能量变小, 加工速度会明显下降。当IP 过小时, 会导致放电能量大幅减小; 当IP 过大时, 放电能量显著增大, 会引起电极丝断丝现象, 这些都会导致加工速度降低。增大WT可明显减小切缝宽度, 但WT 的极限值受电极丝可承受的最大张力限制。
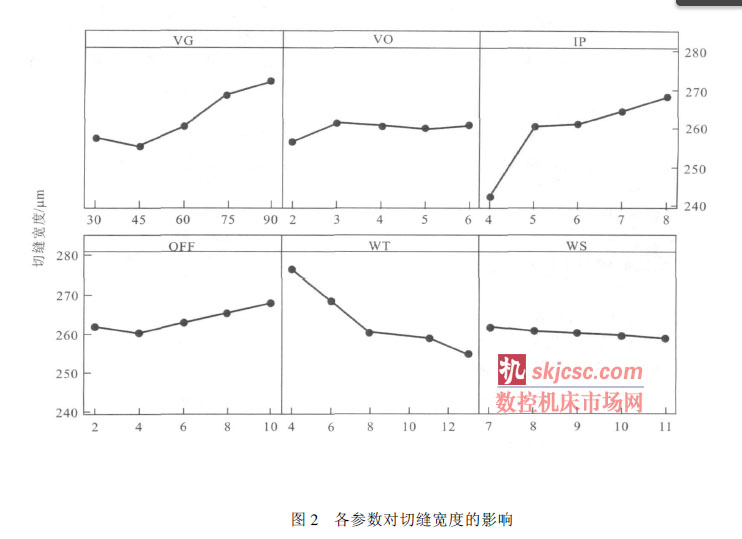
2. 2 电参数对加工时间与表面粗糙度的影响分析
图3~ 图6 分别是伺服基准电压、开路电压、脉冲峰值电流、脉冲间隔对加工时间、表面粗糙度的影响规律。从图中可看出, IP、OFF 对加工时间与表面粗糙度影响显著, VG 影响次之,VO 影响最弱。
IP 与OFF 是电火花线切割平均放电能量的决定因素。在一定的范围内, IP 的增大与OFF 的缩小都会增大平均放电能量, 提高加工效率, 缩短加工图5.6时间, 同时放电能量的增加也增大了单脉冲材料去除量, 使单脉冲电蚀坑变深、变大, 而线切割加工表面由大量电蚀坑组成, 因此, 加工表面粗糙度值会大幅增加。反之, IP 减小、OFF 增大会造成加工时间的延长与表面粗糙度值的下降。IP 过大, 单脉冲放电能量显著增加, 电极丝上分配到的能量相应增加, 极易造成断丝。OFF 过大, 可进行正常加工, 但加工时间会大幅增加; 而OFF过小, 会因极间电蚀产物来不及排除, 引起消电离甚至断丝, 使加工无法正常进行。
在一定范围内调整VG, 电火花加工状态变化不大, 因此对加工时间与表面粗糙度影响不明显; 但过小的VG 易引起短路、断丝, 过大的VG 则会造成开路频率增加, 这些都会明显延长加工时间, 甚至无法正常加工, 但对表面粗糙度的影响较弱。开路电压VO 仅对电介质的击穿有一定影响,对脉冲能量无太大影响, 所以其对加工时间及表面粗糙度的影响很小。
2. 3 非电参数对加工时间与表面粗糙度的影响分析
电极丝张紧力与走丝速度为两个重要的非电参数, 其变化对脉冲放电能量没有影响, 故对加工时间与表面粗糙度影响较弱。图7 与图8 分别是电极丝张紧力、走丝速度对加工时间及表面粗糙度的影响规律曲线。从图7 可看出, 随着电极丝张紧力的增加, 加工时间有所缩短, 主要是因为电极丝张紧力增加有助于减小切缝宽度, 在材料去除率不变的情况下, 切缝宽度减小, 加工速度增大, 加工时间缩短。
3 结论
( 1) 切缝宽度由电极丝直径、电极丝振幅及放电间隙三部分组成。
( 2) VG、IP 与WT 对切缝宽度有显著影响, VO、OFF 与WS 对切缝宽度影响较弱。在一定范围内缩小VG 和IP、增大WT 有助于减小切缝宽度。
( 3) 电加工参数中, IP、OFF 对加工时间与表面粗糙度影响显著, VG 影响次之, VO 影响最弱。
( 4) 增加WT 会使切缝宽度减小, 在放电脉冲能量不变的情况下, 有助于减小加工时间, 提高平均加工速度。
以上实验及讨论不仅适用于铜钨合金, 对一般材料的线切割加工工艺规律也有相应的参考价值。